Rocker Bogie Synthesis
An informal report on the methodology can be found here
Aim -
To design an optimised rocker bogie traversal system for Team Anveshak's 2020 rover. (Team Anveshak is a group of passionate students based in IIT Madras who build Mars rover prototypes and compete in events such as the University Rover Challenge (URC) organised by The Mars Society.)
Summary -
A robust suspension system is key to ensure the successful operation of a Mars rover over rugged terrain. Many types of suspension systems exist, out of which, the rocker bogie suspension system is a popular choice on rovers. It has been NASA's preferred suspension system on all of its past Mars rovers. This isn't a surprise, given the simplicity and efficacy of this suspension system. The rocker bogie suspension system comprises of mechanical linkages alone and does not involve any springs. With the help of a differential mechanism, the rocker bogie suspension system ensures that all wheels of the rover always contact the ground. The objective of this project was to design and manufacture a rocker bogie suspension system.
​
To do this, the 'bumpiness' of the ride was minimized on varying the parameters of the suspension system. Geometric constraints were specified to fix some parameters of the suspension. The other free parameters were varied systematically and the best combination was chosen. The approach used was to reduce the coefficient of variation of the y-coordinate of the rover's center of mass as it moves along a sinusoidal profile. The implementation of the optimization was carried out on MATLAB. Since only two parameters were unknown, a simple brute force method was used to vary the parameters.
​
​

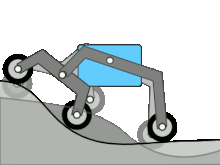
Fig 1a: Animation of the rocker bogie mechanism.
Fig 1b: The final manufactured rocker bogie mechanism on the rover
At the end of the analysis, we concluded that a relatively large span of values of link lengths and angles would satisfy the necessary criteria without sacrificing performance. Finally, the parameter set with the lowest center of gravity was chosen as the final design. The next step was designing the suspension system with the chosen parameters. Finally, the rocker bogie was custom manufactured. The linkages of the rocker bogie system were made of carbon fibre and the coupling units were made out of aluminium.
​
It was observed that the suspension system proved to be very robust and it performed flawlessly at the Indian Rover Challenge 2020. I also presented this methodology of the rocker bogie suspension's analysis and design at the South Asian Annual Mars Convention held as part of the competition.
Fig 2: Animation on MATLAB as part of the analysis
What I learnt -
-
Application of MATLAB to model a real world system
-
Optimization of a real world system on MATLAB
-
Design on fusion 360
-
FEM simulations on fusion 360
-
Integrating components with other sub-modules of the team
-
Ensure low weight and ease of manufacturing
-
Overlooking the manufacturing process
Progress and Current Status -
-
Successful implementation
-
Flawless performance at Indian Rover Challenge 2020
Rough Timeline -
-
Project started - Mid-July
-
Design completed - Mid-August
-
Manufacturing completed - Early December